Article in Holzkurier, issue 17, April 25, 2024 Text and image: Raphael Kerschbaumer and TimberTec
("A world without (SIPal)? Would be unimaginable today...") This is what daily users of the SIPal software solution from TimberTec say. The logistics program is already in use at over 80 company locations in Scandinavia and the number is constantly increasing. Cost reductions and improvements in the entire goods management including production and logistics planning are convincing in Sweden and beyond.
JGA is one of the most satisfied SIPal users in the south of Sweden. Founded in 1928, the family business is now run by the fourth generation. JGA employs a total of around 150 people at its two sites and primarily manufactures high-quality construction products for international customers in Europe, the UK and the USA. With an annual production volume of 250,000 m3, the logistical effort in the sawmill is correspondingly high. "Here in the region, almost all companies rely on SIPal. That's how we became aware of the solution and didn't think twice about introducing the software here," reports Magnus Ragnarsson, Production Manager at JGA.
Exploiting undiscovered potential
"Many sawmills give little or no thought to their internal logistics because they don't see it as something they can easily and simply optimize and improve," says Anders Marklund, Managing Director at DataPolarna, and continues: "This is exactly where we come in with SIPal. Logistics is a major cost factor for sawmills and timber processing companies, which we can reduce by an average of 20%. This means, for example, fewer forklifts in daily use or an increase in production without having to upgrade package logistics."
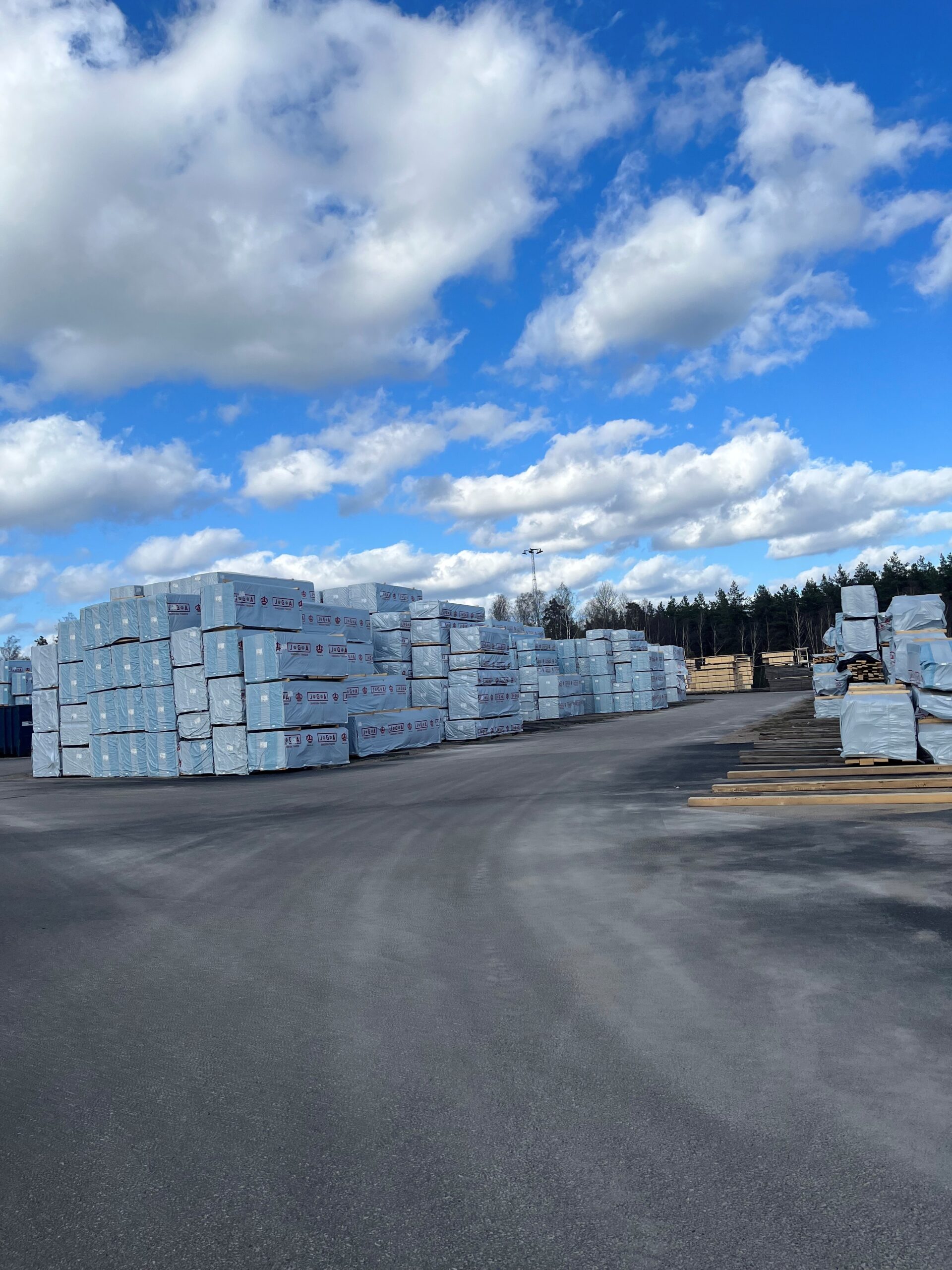
Focus on international exports: JGA produces more than 250,000 m3/year of sawn timber, 70% of which is exported internationally.
Employees are enthusiastic
The list of benefits that SIPal offers its users is long. JGA implemented the program back in 2018 and today, almost eight years later, the software has become an integral part of employees' daily work. "A world without SIPal would be unimaginable," is how one JGA employee aptly puts it. Holzkurier meets the long-serving forklift driver as he is transporting a package of sawn timber from the dry sorting area to the warehouse. Thanks to SIPal, he not only knows which package it is, but is also assigned a suitable storage location at the same time, which can be set and defined according to customer-specific rules. "The entire company premises can be digitally mapped in SIPal. Depending on the assigned properties of the products, such as dimension, quality or destination country, the entire warehouse management can be optimized quickly and easily. In addition, the employee saves a lot of time, as there is no need to search for package or storage locations," explains Marklund.
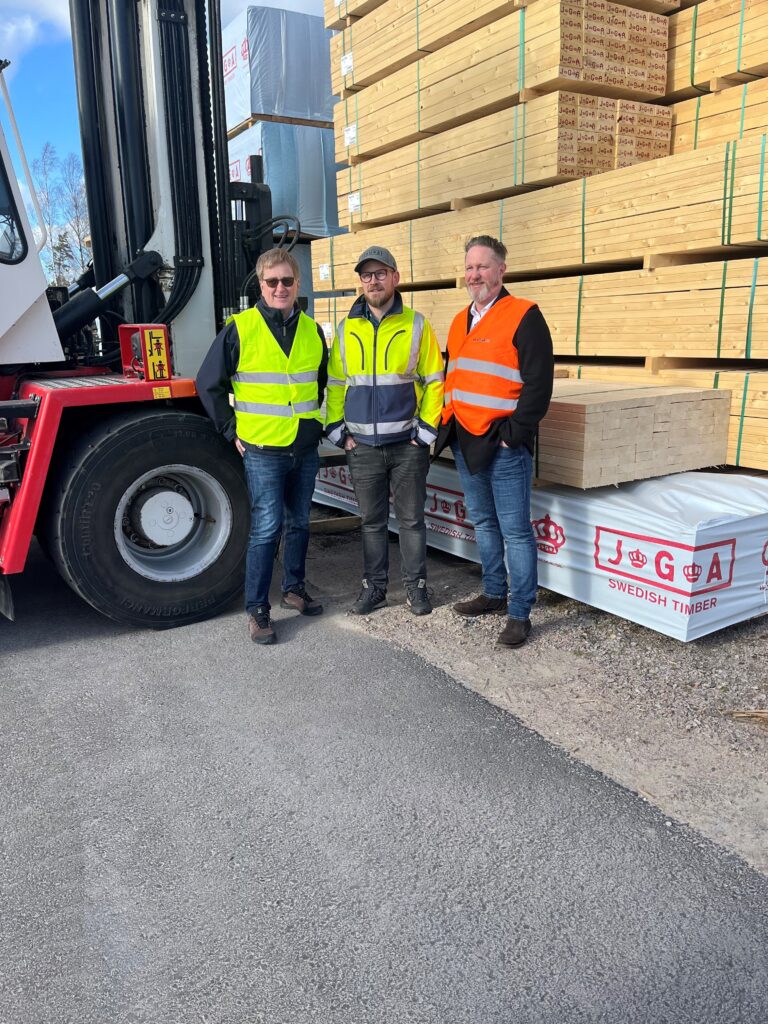
No more convincing necessary: JGA production manager Magnus
Ragnarsson (center) is convinced by SIPal with DataPolarna managing director
Anders Marklund (left) and Per Durlind, sales and marketing manager at
TimberTec (right).
Solutions without satellite connection
An RFID tag is installed in the floor in front of each storage location. The system is supplemented by an antenna, mounted on the underside of the truck, and a board computer that can also be used offline
. Together, they ensure that the forklift driver knows exactly where he is at all times and where the package should be placed accordingly. This significantly reduces the likelihood of errors. "During implementation, we spent a few days drilling holes in front of the individual storage locations and placing the RFID tags accordingly. Once attached, they last a lifetime," says Ragnarsson, describing the few technical requirements that the system needs. The RFID solution has additional advantages, as Marklund explains: "Our solution works without GPS. In sawmills, forklifts constantly move back and forth between the indoor and outdoor areas or move around in drying chambers. GPS connections often break down, but an RFID tag in the floor is always recognized."
Influence goes beyond logistics
The JGA management team is equally enthusiastic about the logistics tool: "We constantly receive great feedback from our employees, but we also benefit greatly from SIPal in sales and production planning. We know exactly what is in stock at all times and can therefore quickly and easily keep track of our entire inventory. This also has a positive effect on production planning, which can be much better controlled and adapted to requirements by looking at the system. Before SIPal, we also had a number of packages every year that we simply didn't know where they were. This can no longer happen to us," says Ragnarsson.
Straightforward upgrade for existing customers
SIPal works independently of the customer's ERP system. "Implementation is particularly easy for TimberTec customers, as they can use the new standard integration between TiCom and SIPal," says Marklund. "With TimberTec, you have a single provider for ERP and logistics and can make optimum use of all the resulting synergies." TimberTec has a large customer base in Central Europe in particular. Since the acquisition of DataPolarna last fall, SIPal is now also part of the TimberTec family. "SIPal is a must-have for the day-to-day handling of countless timber packages. For existing TiCom customers, our tool raises efficiency to a new level, because the many positive experiences from Scandinavia show what our solution is capable of. The same can also be transferred to the rest of Europe easily, quickly and, above all, efficiently," summarizes the industry expert.